Cellophane
Brief History
Cellophane was invented by Jacques E. Brandenberger . In 1900, inspired by seeing wine spill on a restaurant's tablecloth, he decided to create a cloth that could repel liquids rather than absorb them. His first step was to spray a waterproof coating onto fabric, and he opted to try viscose. The resultant coated fabric was far too stiff, but the clear film easily separated from the backing cloth, and he abandoned his original idea as the possibilities of the new material became apparent
https://upload.wikimedia.org/wikipedia/commons/thumb/e/e8/Xanthogenate_Cellulose_Structural_Formula_V1.svg/300px-Xanthogenate_Cellulose_Structural_Formula_V1.svg.png
It took ten years for him to perfect his film. His chief improvement over earlier work with such films was adding glycerin to soften the material. By 1912 he had constructed a machine to manufacture the film, which he had named Cellophane, from the words cellulose and diaphane ("transparent").
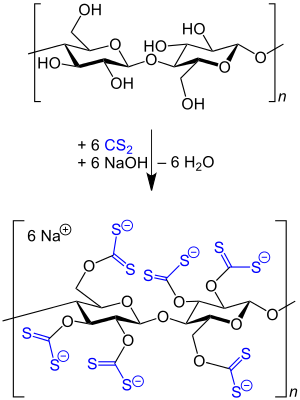
Cellulose is treated with alkali and carbon disulfide to yield viscose.
Cellophane can come in any color and is used in packaging different products in food section industries.
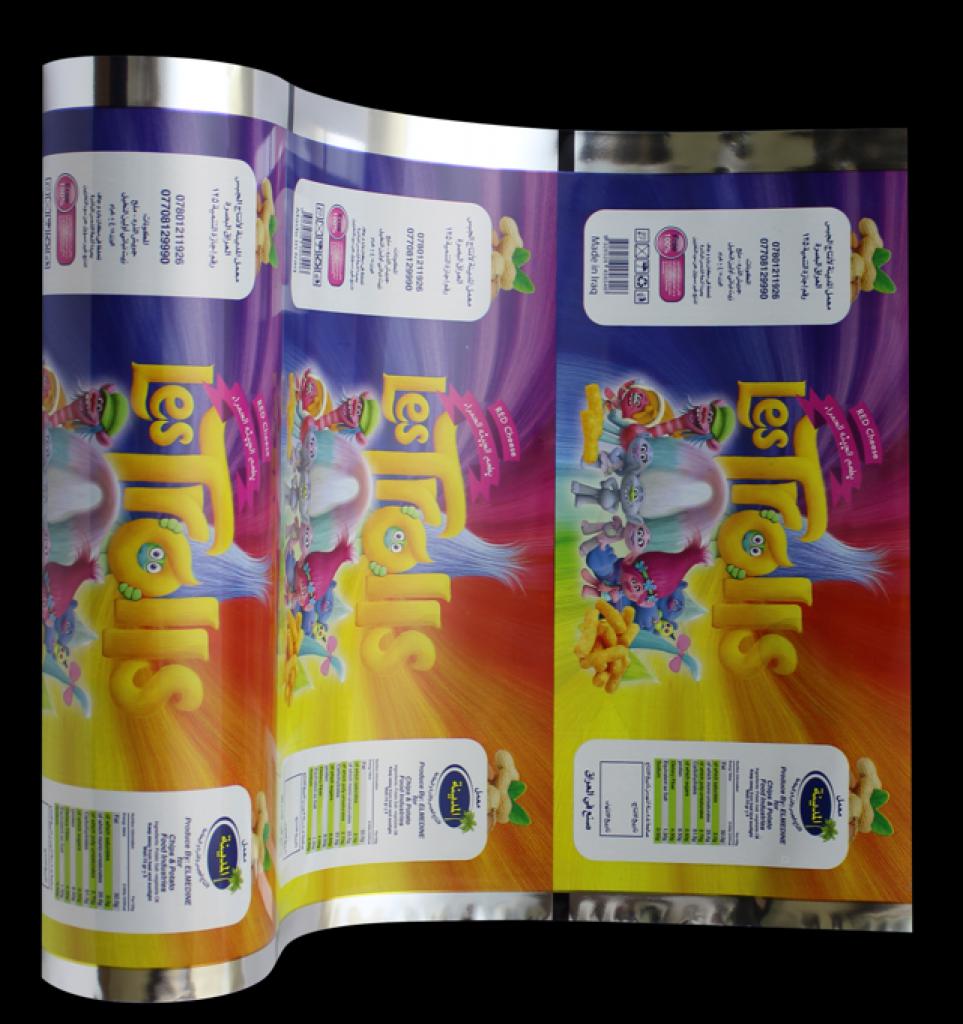
Cellophane is a thin, transparent sheet made of regenerated cellulose . Its low permeability to water, bacteria, oils, greases and gases that makes it useful for food and snack packaging. Cellophane is highly permeable to water vapour, but may be coated with some lacquer to prevent this( usually nitrocellulose).
As well as food packaging, cellophane is used in transparent pressure-sensitive tape, tubing and many other similar applications.
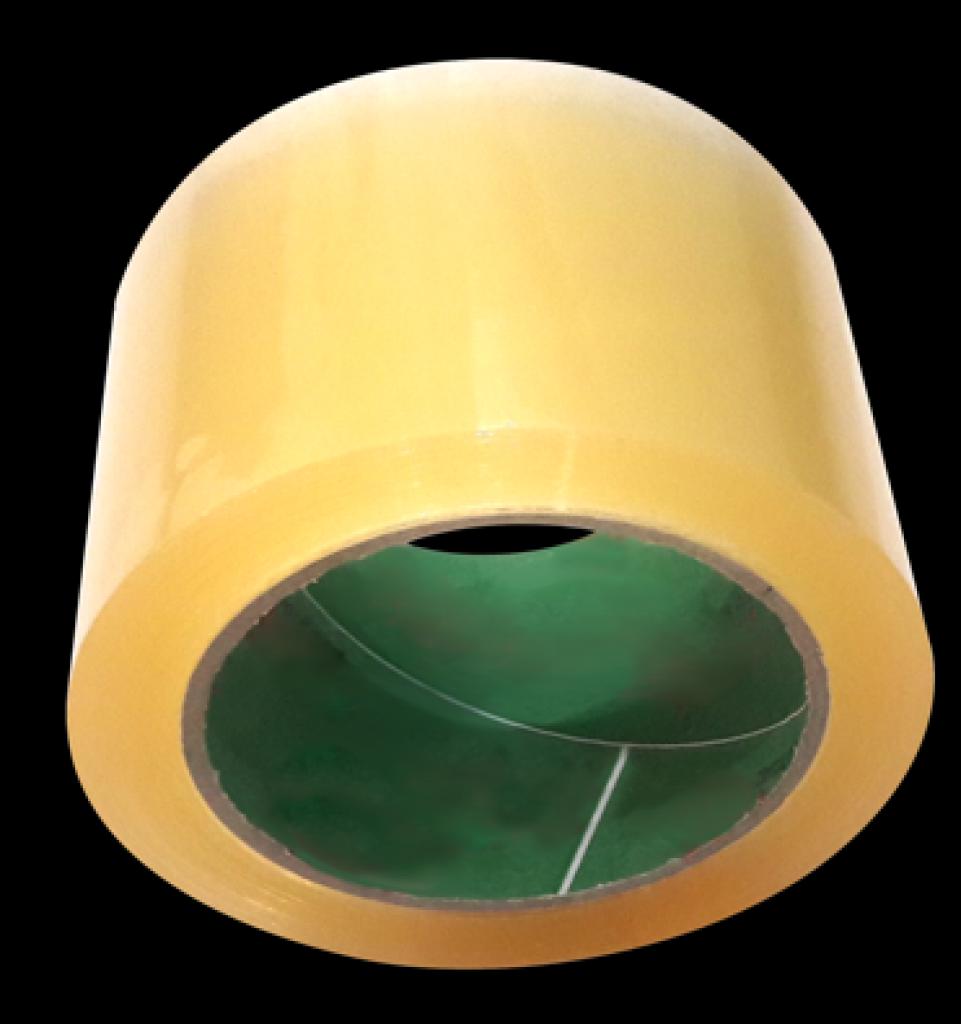
Unlike many other similar materials, cellophane is biodegradable.
Present day
Cellulose film has been manufactured continuously since the mid-1930s and is still used today. As well as packaging a variety of food items, there are also industrial applications, such as a base for such self-adhesive tapes and Scotch Tape, a semi-permeable membrane in a certain type of battery, as Visking tubing, and as a release agent in the manufacture of fibreglass and rubber products. Cellophane is the best material for manufacturing cigar packaging; its permeability to moisture makes cellophane the perfect product for this application as cigars must be allowed to "breathe" while in storage.
Cellophane sales have dwindled since the 1960s, due to alternative packaging options. The polluting effects of carbon disulfide and other by-products of the process used to make viscose may have also contributed to this; however, cellophane itself is 100% biodegradable, and that has increased its popularity as a food wrapping.
Material properties
Cellophane is biodegradable, but highly toxic carbon disulfide is used in most cellophane production. Viscose factories vary widely in the amount of CS2 they expose their workers to, and most give no information about their quantitative safety limits or how well they keep to them.
What is the Bopp?
BOPP is biaxially-oriented polypropylene film. It's made of polypropylene (PP). Polypropylene a thermoplastic polymer, alternately known as polypropene. ... BOPP is essentially polypropylene that's stretched flat to thin film. BOPP is oriented with a system that stretches it in two directions (Machine Direction and Transvers Direction).
Related image
biaxially-oriented polypropylene film is commonly used for applications that require moisture resistance, optical clarity and high tensile strength such as: Food & Beverage & sweet & candy Packaging. Medical Packaging. Personal Care Product Packaging.
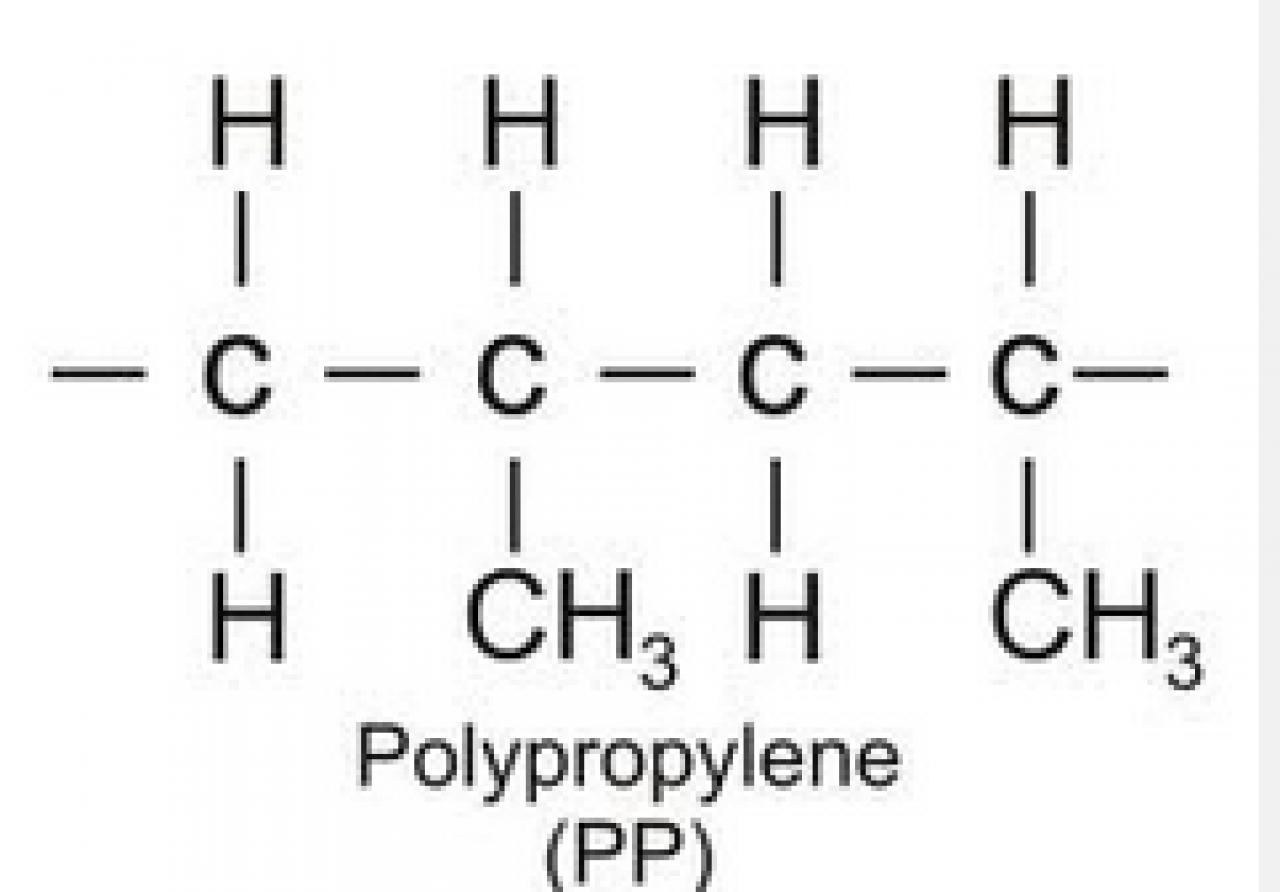
These heat sealable and pearlised films are meant for advanced packaging, labeling and decorative wrap-ups of different products
In all the three, Polypropylene is common which is the basic polymer for the manufacturing of these bags. PP is Polypropylene, OPP is Oriented Polypropylene, and BOPP is Biaxially Oriented Polypropylene. ... However, one can feel the difference by touching as OPP feels brittle whereas PP is softer.
Our BOPP products polymers deliver high quality packaging while improving production efficiency.
Biaxially-Oriented Polypropylene (BOPP) films have become a popular, high growth film on the world market because of a unique combination of properties such as better shrinkage, stiffness, transparency, sealability, twist retention and barrier.
BOPP film is used in a variety of applications including:
flexible packaging
metallising
cable wrap and insulation
pressure sensitive tape
printing and lamination
stationary
flower sleeves
PETRO POLYMER RANGIN KAMAN serves the BOPP market with a homopolymer product in combination with several kind of skin resins. Based on a special molecular structure and stabilisation of the resin, these homopolymers provide optimal mechanical and optical properties, as well as excellent processability.
Polymers offer several advantages to producers, packagers and other users of BOPP film. Its high clarity and low haze help producers of film or packagers to create glossy, high-transparency film that enhances the appearance of packaging or other products.
In addition, we offers high seal strength, even at low sealing pressures and after surface treatment to keep out moisture and contaminants. The polymer also has a high melting point for easy processing combined with a low seal initiation temperature and a wide sealing window thanks to the balanced polymer structure.
Other benefits include:
Low amorphous fraction resulting in low xylene extractables
Low migration for metallised film
Easy stretchability enables fast and smooth processing on high speed Form, Fill & Sealing or other machines
Low tackiness and easy jaw release provide good runnability on packaging machines
Low blooming of amorphous and low Mw (molecular weight) fractions and additives, giving stable surface properties
Tensile Strength |
/ Mpa |
33 |
25 |
Tensile Modulus |
/ Gpa |
1.4 |
1.0 |
Elongation at Break |
/ % |
150 |
300 |
Hardness |
/ Rockwell "R" Scale |
90 |
80 |
Notched Izod Impact |
/ kJm-1 |
0.07 |
0.1 |
Heat Distortion Temp (HDT) |
@ 0.45 MPa / °C |
105 |
100 |
Heat Distortion Temp (HDT) |
@ 1.80 MPa / °C |
65 |
60 |
Volume Resistivity |
/ logÙm |
19 |
19 |
Oxygen Index |
/ % |
17 |
17 |
METALIZED FILM
metalized films are polymer films coated with a thin layer of metal, usually aluminium. They offer the glossy metallic appearance of an aluminium foil at a reduced weight and cost. Metallised films are widely used for decorative purposes and food packaging, and also for specialty applications including insulation and electronics
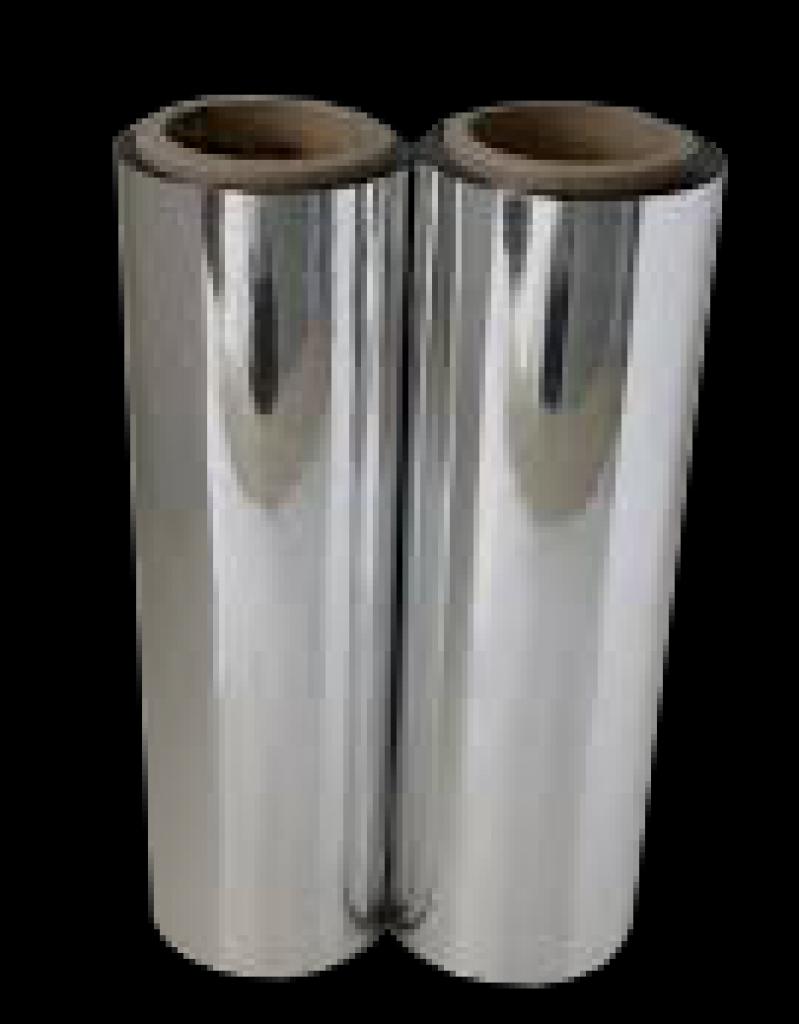
Packaging
Both metallised PET and PP have replaced foil laminates for products such as snack foods, coffee and candy, which do not require the superior barrier of aluminium foil. Metallised nylon and polyethylene are used in the meat export market. The controlled permeation extends shelf life.
Metallised films are used as a susceptor for cooking in microwave ovens.[5] An example is a microwave popcorn bag.
Many food items are also packaged using metallised films for appearance only, as these produce a package with greater sparkle when compared to competing products that use printed paper or polymer films.
Settings
Tags
cellophane wrap cellophane bags cellophane cellophane noodles cellophane fka twigs cellophane tape cellophane meaning cellophane definition cellophane paper cellophane art cellophane amazon cellophane angel cellophane alternative cellophane synonym cellophane and montero cellophane adhesive cellophane at walmart a cellophane bag with 2m sucrose a cellophane is made of a cellophane definition a cellophane treatment cellophane a hamper cellophane a translucent cellophane a transparent material cellophane a sentence cellophane bags for baskets cellophane bees cellophane bags walmart cellophane betta cellophane bags near me cellophane bags michaels cellophane b&m
cellophane wrap cellophane bags cellophane cellophane noodles cellophane fka twigs cellophane tape cellophane meaning cellophane definition cellophane paper cellophane art cellophane amazon cellophane angel cellophane alternative cellophane synonym cellophane and montero cellophane adhesive cellophane at walmart a cellophane bag with 2m sucrose a cellophane is made of a cellophane definition a cellophane treatment cellophane a hamper cellophane a translucent cellophane a transparent material cellophane a sentence cellophane bags for baskets cellophane bees cellophane bags walmart cellophane betta cellophane bags near me cellophane bags michaels cellophane b&m
Related Content
User notes
Insert a note
: