Different degrees of anilox rollers
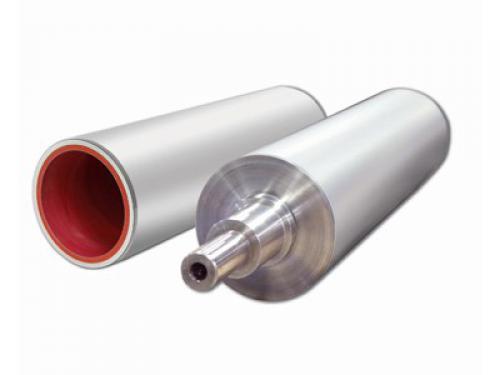
Different degrees of anilox rollers
It is essential for all flexo printers that the anilox gives the correct ink density from the first print and stays consistent throughout the whole run regardless of which cell structure or shape is used, and the anilox manufacturers are going to great lengths to achieve this
n recent years the flexo print process has enjoyed a period of persistent growth thanks to new advancements in ink, anilox and plate technology, as well as printing presses. These improvements have elevated flexo reproduction capabilities far beyond what has traditionally been possible and put flexo on a similar level to offset and gravure printing techniques.
Printers and converters today are under pressure to achieve consistency and repeatability, with everything from ink viscosity, dot gain and density, to feeds, speeds and waste being measured and analysed, and the ink transfer from the anilox is scrutinised now more than ever.
every anilox surface is measured using a non-contact surface finish instrument and the Roughness Average (RA) is recorded. RA measuring gauges are used to measure roughness after polishing and before the surface is engraved. The lower the RA number, the smoother the component. Every anilox roller manufactured by Harper, regardless of specification, must have a RA of 3.0 or lower before being engraved.
The base of the anilox is a steel roll, which then has a ceramic, titanium and water mix sprayed over it. This is then fused to the base using a flame. Once the ceramic is built up, it needs to be smoothed down. Smoothness is the most important aspect of any anilox roller, but when using a material as hard as ceramic there is only one substance that is physically able to do this, namely diamond.
Settings
Tags
anilox rollers anilox roller cleaning anilox roller manufacturers anilox roller cleaning machine anilox bcm anilox anilox roller for flexo printing anilox roller cleaner anilox roller repair anilox roller definition anilox roller cleaning chemicals anilox roller apex anilox roller application anilox rollers south africa anilox roller lpi and bcm alt anilox rollers the anilox rollers anilox roller bangalore anilox roller bcm anilox roller buyers in india
anilox rollers anilox roller cleaning anilox roller manufacturers anilox roller cleaning machine anilox bcm anilox anilox roller for flexo printing anilox roller cleaner anilox roller repair anilox roller definition anilox roller cleaning chemicals anilox roller apex anilox roller application anilox rollers south africa anilox roller lpi and bcm alt anilox rollers the anilox rollers anilox roller bangalore anilox roller bcm anilox roller buyers in india
Related Content
User notes
Insert a note
: